针对IMG阴模真空成型软质仪表板的常见外观缺陷进行分析和对策讨论,从设备、模具、材料、工艺等各方面提出了相应的优化措施。通过综合考虑阴模真空成型各工艺过程的特点,为解决软质化仪表板的外观品质缺陷提供了较好的解决思路和具体的优化措施。
目前软质仪表板生产工艺有多种,如搪塑成型、IMG(InMoldGraining)阴模真空成型、PU表皮模塑成型等。其中,IMG阴模真空成型以皮纹均匀、耐久性高、低气味散发和相对较低的成本等特性得到广泛应用[1]。国内用于生产汽车仪表板的IMG阴模真空成型设备、模具及材料大都依赖进口,现有的文献资料也都以介绍工艺原理及应用为主,有关IMG阴模真空成型工艺质量控制的研究报道较少。本文针对IMG阴模真空成型软质化仪表板在调试和生产过程中常见的外观缺陷进行分析,并提出了改善方法。
IMG阴模真空成型工艺简介
IMG阴模真空成型,是一种热成型技术,在汽车行业中多用于软质化仪表台和车门内饰板的生产加工。该工艺由真空成型设备(提供成型所需真空力、上下台面动作、表皮框动作、表皮上料、表皮加热等功能)、镍壳真空模具、骨架以及附带背胶的表皮组成。其生产流程如下:先对骨架和表皮进行预加热,然后将骨架安装在真空模具的下模凸腔上,与受热延展的表皮一起在镍壳真空模中合模。接下来通过真空负压使上模凹腔镍壳上的预制皮纹转印到表皮上,同时表皮的背胶与骨架因负压和锁模压力而紧紧粘附,从而生产出有表皮包覆的仪表板部品,阴模真空成型工艺原理见图1。
图1 阴模真空成型工艺原理
常见外观缺陷及对策
IMG阴模真空成型软质仪表板的常见外观缺陷有/形状/皮纹转印不清晰、褶皱/破损、塌陷/凹陷、鼓包/粘合不良等,具体见图2。下面分别阐述各项不良的影响要素和施策方向。
图2 常见外观缺陷
形状/皮纹转印不清晰
表皮本身是光滑的片材,真空成型时靠设备加热软化延展,然后被真空负压紧密吸附在镍壳真空模型腔面上,从而转印出与镍壳相同的形状和皮纹。因此与形状/皮纹转印清晰度相关的主要因素有表皮延展度、成型真空度(负压值)和镍壳的加工精度等。
1、表皮延展度
表皮延展度的控制条件有表皮加热温度和表皮物性。表皮加热温度越高,其延展度和软化程度越好,在同等真空负压条件下转印的形状/皮纹也越清晰。可以通过调整表皮加热炉的加热器温度和加热时间来控制表皮温度。如果表皮温度太低、延展度不足,在合模时表皮就无法包裹住骨架或型腔,不能形成有效的密封负压进行成型;同时表皮表面不够软化也不利于皮纹/形状的转印。如果表皮温度太高,会造成过度延展在成型过程中形成褶皱或破损。使用的表皮都是TPO材质,其加热温度控制在190~210℃时延展度较为适中、转印效果较好,转印皮纹深度随表皮加热温度的变化见图3。
表皮物性一般在表皮开发时由材料厂家进行调整,量产应用中极少改变,本文不做叙述。
2、成型真空度
成型真空度由真空成型设备和模具来共同保证。真空成型设备上设置有真空罐和真空泵组成的真空系统,镍壳模具上在型腔周边设置有密封筋。成型时上、下模合模夹住表皮,配合密封圈使型腔内部形成密封,通过设备端的真空系统将模具型腔抽成负压,从而进行真空成型。型腔内的负压高,则表皮与上模镍壳贴合更紧密,有利于皮纹/形状的转印;负压低则反之。
图3 转印皮纹深度随表皮加热温度的变化
使用的真空成型设备可提供最大约-100KPa的真空负压。模具型腔内的负压则与模具本体的密封性相关。由于模具是由多个部分镶拼而成,各镶件部分的研配间隙需要精确控制并使用耐候油脂或硅胶密封。模具密封不良会导致成型过程中真空负压不足,所以新模具调试前应仔细排查确认有无真空泄漏点[2]。模具型腔内负压在-50KPa以上时,一般面皮纹和形状可以实现良好的转印再现,转印效果随真空度的变化如图4所示。
真空度-30KPa
真空度-70KPa
图4 转印效果随真空度的变化
3、镍壳加工精度
IMG阴模真空成型模具中镍壳的加工精度一般通过电铸工艺来保证。目前在电铸镍壳模具制造工艺领域国外处于领先地位,并且对此技术保密,鲜有报道。国内用的阴模真空模具绝大多数是从日本、德国等发达国家进口。国外模具厂家都有保证镍壳加工精度的相关技术和专利,本文不做叙述。由于电铸工艺的特殊性,现阶段技术条件下镍壳加工完成后如改修,一般需要返厂家处理。所以建议在镍壳的加工过程中,对每次翻模的造型及皮纹再现情况都进行确认。一旦模具运抵现地,后期再返厂维修,时间损耗巨大。
4、其他因素
除了以上主要因素,产品外观的形状/皮纹转印不清晰还与成型时的上模模温和上下模间隙有关。较高的上模模温更利于形状/皮纹的再现,我司的工艺标准是上模模温85℃。上下模间隙是决定阴模真空成型制品品质的关键。合适的上下模间隙在合模时能够给TPO表皮适宜的压力,配合上模真空形成的负压,清晰拓印出镍壳的形状和皮纹。模间隙过大对形状/皮纹再现不利;模间隙过小则会出现褶皱不良[3]。关于模间隙的调整下文会有详细介绍。
表皮褶皱/破损
表皮褶皱和破损通常是由表皮延展度过大和模间隙过小的双重作用产生的。表皮延展度过大会造成表皮在加热过程中过度下垂拉伸,合模时多余的表皮被重叠挤压在有限的模具间隙内会形成褶皱。另外,表皮过度拉伸,其厚度变薄,在合模过程中易被骨架或模具型腔的尖锐处刮破,尤其在模间隙小处。通过降低褶皱/破损对应部位的表皮加热温度可以改善不良,但为了保证形状/皮纹的转印清晰,温度降到一定程度(约190℃)就不建议继续下调,所以大多数场合主要靠调整上下模具间隙来应对。
为更好控制模具内间隙,在调试前应对模具间隙进行测量。选取下模具至少10个横截面,在每一个横截面的曲面变化区域设置至少一个测量点,应覆盖所有品质重点区域,如安全气囊区域、仪表罩区域、倒扣区域。在测量点上放置油泥,通过测量合模后油泥的厚度来确认模内间隙量。如图5所示,模具内间隙测量分为无骨架模具内间隙(下文简称间隙A)和有骨架模具内间隙(下文简称间隙B)两种数据。前者用于调整模具本身改修量,后者用于调整骨架改修量。无论是间隙A还是间隙B,由于上模镍壳无法简单打磨或烧焊,模内间隙调整只对下模或骨架进行改修。为了避免重复调整,提高改修效率,模间隙调整建议按照先间隙A后间隙B的流程实施。原则上我们倾向于调整基材而不是镍壳真空模具本体,模具内间隙调整的依据是产品品质,因此需要大量时间进行反复的测量和改修,直至获得合格产品。一旦获得合格产品,应将此时模具内间隙数据记录存档。
图5 模内间隙
1.间隙A调整
间隙A的影响因素:
a.上下模设计间隙;b.上下模型腔面加工精度。
首次真空成型调试时,在成型出样之前就应当对间隙A进行整体测量把握,建议按照设计值±0.5mm进行管理。如果间隙趋势整体偏小或偏大,可以通过真空成型设备调整上下模的合模距离。局部偏小或偏大时,需要对下模对应的区域进行打磨或修补。间隙A调整到设计值±0.5mm以内之后,如仍有褶皱/破损缺陷发生时,则需要对间隙B进行确认和调整。
2.间隙B调整
间隙B的影响因素:
a.骨架精度(大小、肉厚、变形等);b.骨架与真空模具下模的贴合度。
骨架为注塑成型产品,精度的影响因素较多,包括注塑成型(模具加工精度、收缩率、成型工艺、收缩变形等)、保存姿态(搭载姿态、放置时间等)和真空成型前预加热(加热温度、加热时间、加热姿态、二次收缩等)。安定的骨架尺寸是保证品质解析的重要前提,在真空成型调试之前应该对骨架以上所有因素进行逐项的测量和确认,保证骨架尺寸符合图纸各项要求。本文不对骨架精度的品质保证方法进行叙述。
在测量间隙B之前,应对骨架与下模的贴合度进行确认。有时骨架背面与真空模具下模存在干涉,在干涉部位骨架无法与下模良好贴合,会导致间隙B偏小。可以借助红丹观察骨架与下模的贴合状态,其原理与注塑模具研配时利用红丹确认分型面的贴合相同。
操作步骤简述如下:
a.骨架预加热,温度条件与生产一致;
b.在骨架冷却收缩之前,迅速在骨架背面均匀涂上红单;
c.将骨架扣在下模上,用软锤敲击骨架正面;
d.顶出骨架,观察留在下模上的红单印记。
下模无红丹的部位表示附近有干涉或是下模过切。
当发生褶皱或破损缺陷时,应确认褶皱部与周边未褶皱部的间隙A、B值及红单状态。通过对比数值偏差决定下模的打磨量。下模打磨量确认后,建议在骨架背面对应的部位进行临时的减胶验证,如效果OK再实施下模打磨。打磨量一次性不易太大,0.2-0.3mm为宜。每次打磨后再次成型确认品质状态,如不达标则重复进行红单和间隙的确认,直到品质合格为止。模间隙的测量及调整是软质仪表台品质解析过程中耗时最长的步骤,需要反复测量和验证。为了避免测量手法的误差,测定人员最好固定。
塌陷
塌陷多见于产品造型尖角处或骨架真空孔处,发生原因即上下模间隙过大或真空孔直径过大。模间隙过大需对下模或者骨架进行修补,造型尖角塌陷一般对骨架进行加胶处理,尖角塌陷对策如图6所示。骨架上真空孔的直径一般推荐Φ0.5-1.0mm,设置过小注塑模具的强度难以保证,设置过大(≥Φ1.5mm)容易在下模抽真空时形成凹坑塌陷。
图6 尖角塌陷对策
鼓包/贴合不良
软质仪表板在成型后需要进行高温烘烤检查,如果烘烤后表面出现鼓包,或是铲除表皮后发现骨架上有明显漏黑,则表明此处的表皮和骨架未能完全贴合。贴合不良的产品如流入市场,将在高温环境下出现仪表台鼓包的品质缺陷。困气是造成贴合不良的主要原因。真空成型过程中,表皮背胶在高温状态下被激活,如果上下模合模时表皮和骨架之间还有空气未被负压排出,被困空气会在表皮与骨架之间形成气膜导致表皮无法与骨架粘合。遇高温时被困空气受热膨胀,在产品表面形成鼓包。
上下模合模速度和骨架表面真空孔与排气纹的分布直接与困气关联。一般而言适当降低合模速度能改善困气,但是要牺牲生产节拍。所以骨架表面真空孔与排气纹的合理设置是解决困气鼓包的关键。
真空孔分布的方法是在曲率变化小的表面分布较少、间距大;曲率变化大的表面,如圆角、型面变化处等分布较多、较密集[4],骨架表面真空孔分布见图7。真空孔的孔径及分布一般在骨架注塑模具设计时已经决定,如果在真空成型时发现有鼓包不良,可以在骨架的对应部位临时用钻头加工真空孔验证效果。
图7 骨架表面真空孔分布
某些部位骨架无法设置真空孔,则需要调整排气纹路提高排气效率。排气纹的深度、间隔以及与真空孔相连的距离都会影响排气效率。两家阴模真空成型模具供应商分别使用不同的排气纹设计,骨架表面排气槽情况如图8所示。实际运用中A式样排气纹虽然较深,但实际排气效果不如B式样。但在A式样排气纹上追加横向纹路后,排气效率可达到B式样同等水平。
图8 骨架表面排气槽
缺陷要因总结
通过以上简述,常见的IMG真空成型外观缺陷的要因。见表1。
表1 外观缺陷要因表
结论
IMG阴模真空成型是一项涵盖了设备、模具、材料及工艺的复杂工艺技术。其产品品质解析需从多个领域展开复合分析。造成不良的因素互相之间存在关联,如何在各个因素之间取得平衡得到最优品质离不开大量的数据分析和经验积累。针对某项缺陷进行了对策调整后,要注意确认是否带来其它的问题。以上所述仅为常见缺陷的解析方法,实操过程中需要结合具体情况展开深入分析。软质化仪表板将成为今后主流汽车内饰的发展方向,我们应当加强对IMG阴模真空成型工艺的了解与研究,进一步提高IMG阴模成型软质化仪表板的品质解析效率。
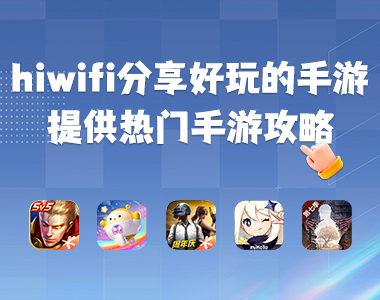